Pla Broke Inside Feed Delta Mini
You're in the middle of a long 3D print and you start hearing a click-click-click coming from your extruder and notice filament has stopped extruding. Chances are, your printer is experiencing a jam. If you act fast, you can pause your print and recover the job with minimal artifacts, but in many cases often counts as a print failure and will require canceling the print and performing some maintenance. Jams and clogs happen to every maker and thankfully they can be fairly easy to fix!
Before we begin, it's important to define each of the parts we're talking about as the wording can get a little confusing. We'll be focusing on the extrusion assembly which consists of two parts; a hot end and an extruder.
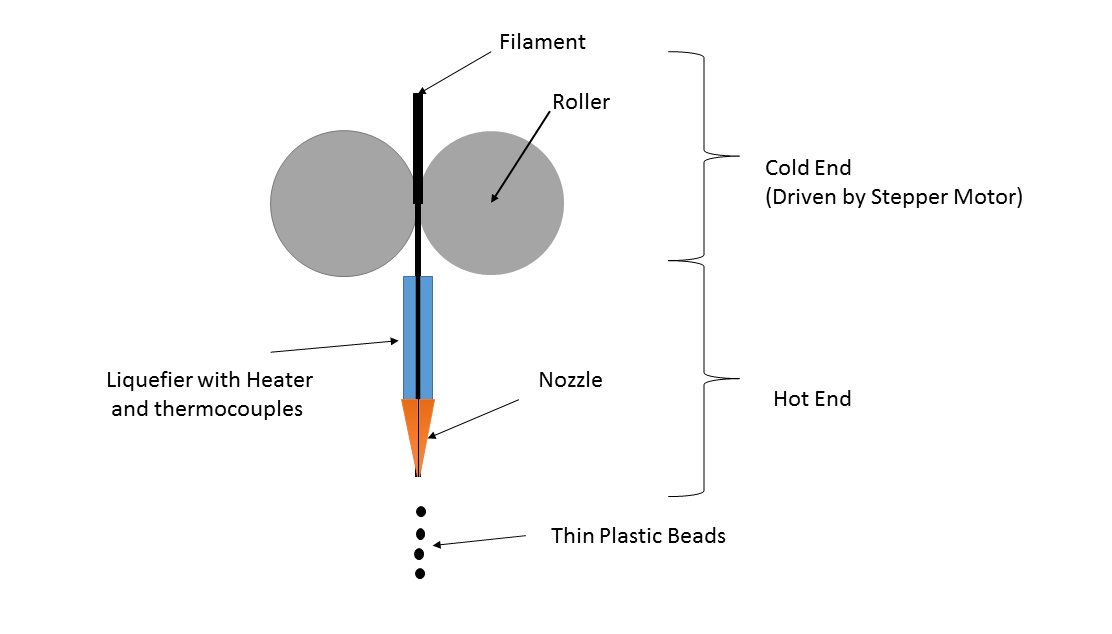
Image from wikimedia
The extruder is what actually pushes the filament forwards. Filament is sandwiched between a gear and a bearing (or sometimes another gear for more grip, like with Bondtech) and is forced forwards by a stepper motor. After it exits the gears of the extruder it is fed toward the hotend.
There are two types of extruders – bowden and direct. A direct drive extruder sits directly above the hot end and forces filament straight through; a direct drive is mounted directly on the moving print head. A bowden extruder is usually attached to the frame of the printer and leads the filament through a thin teflon (PTFE) tube called a bowden tube until it reaches the hot end.
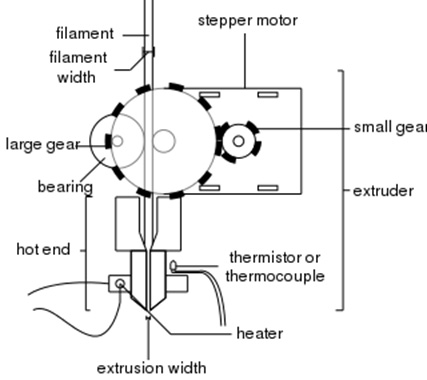

When filament gets stuck, it's either in the melt zone or nozzle section of the hot end and not usually at the extruder. You may seldom encounter jams in the extruder due to oversized filament that's significantly larger than nominal (filament measuring 2.0mm but should be 1.75mm) and can't enter the extruder, so it jams. Otherwise, a jam will occur within the hotend for several reasons. Now that we're clear on what parts of the printer we're dealing with, let's take a look at some of the symptoms and causes of a jam.
5 Causes of 3D Printer Jams and How to Fix Them!
When your hotend is jammed, you might notice less filament coming out of the nozzle or no filament at all! Here are a few of the more common causes:
1) Heat Creep: It may sound counter-intuitive, but if the hot end isn't cooled properly, filament starts getting viscous too high up in the hot end and we run into an issue called heat creep. This is when filament liquefies too early and in a portion of the hotend that cannot actively be temperature controlled. The "cold end" is where the heatsink is kept cool by a fan and if that fan isn't strong enough or it's pushing warm air already (in the case of an enclosed printer), there isn't enough airflow to properly keep it cool and heat "creeps" up from the hotend slowly.
The Fix: You'll generally hear your extruder motor grinding or clicking when filament is jammed and if that's the case, stop the print and remove the filament. Make sure the cooling fan for your hot end is running properly and ensure that the heat sink and heater block are securely attached. In the case of hot ends like the E3D V6, it helps to apply thermal paste to the threads of the heat break that screw into the heatsink. If you're printing in an enclosure with a material not traditionally printed in an enclosure (like PLA) it is much more likely to cause a jam; open the door or take off a side panel to allow enough cool air into the fan. Still having issues? Check that your retraction distance isn't set too high and pulling hot filament up into the cold end where it cools down.
2) Hot end temperature is too low: If your hot end temperature is too low, filament isn't molten enough and creates a lot of resistance within the nozzle until it reaches a critical mass and can't be fed through the nozzle. This causes the extruder to grind away at the filament, creating a flat spot and making it even more difficult to extrude.
The Fix: Check the temperature specifications for your specific filament. PLA 3D printing filament likes to extrude around 200°C and ABS 3D printing filament around 245°C. If you're having issues with the listed specifications, try increasing the temperature by 5 degrees at a time, making sure not to exceed the maximum temperature of your hotend of the recommended temperature range of the filament.. When switching filaments, make sure all of the previous material is purged after changing temperatures. Using a nozzle larger than 0.4mm or layers thicker than 0.3mm might mean you need to increase temperatures past the maximum recommended temperature to get your filament molten enough to be extruded reliably, as you are extruding a lot more filament in general.
3) Nozzle too close to bed: If the nozzle is too close to the bed, there's no room for filament to be extruded out the nozzle and this causes a jam.
The Fix: Make sure you have a properly leveled bed. Check out MatterHackers' Bed Leveling Guide to get the best first layer for your print here.

Image from Ultimaker
4) Inconsistent Filament Diameter: Most filament manufacturers say their filaments is within 0.05mm of the listed extrusion width (usually 1.75mm or 2.85mm). If your filament deviates too much from the specification, it can have issues being fed through the hot end.
The Fix: If you suspect this is happening, break out a pair of calipers and measure the filament at several random locations to see if it's up to spec. In some cases filament might be perfect along the entire length except for one small bulb that stops you in your tracks. If your filament diameter is consistently off and you encounter these bulbs regularly, it might be time to consider a new brand.
You can always find quality, and precise filament at MatterHackers – their PRO Series line of filament is dimensionally stable, boasting ±0.02mm diameter tolerance and precise color consistency. Also, check out their MH Build Series materials – it's a top-tier material and at a very affordable rate – you can get PLA filament as low as $16.17 with bulk pricing.

Image from Simplify3D
5) Dust or particles: Dust or other small particles might decide to hitch a ride on your filament until they reach your hot end and burn causing an unfortunate clog.
The Fix: Unclog your Nozzle Using the Cold Pull Method – see below for a more detailed break down of how this works, or visit this article from our friends at MatterHackers. Running your filament through a piece of sponge if your filament is noticeably dusty is a reliable way to clean off dusty filament before it jams you up.
3 Steps to Unclog your Nozzle with the Cold Pull Method
Some articles recommend using a blowtorch or drill to clean your nozzle. For those of us that can't be trusted with power tools, fire, and chemicals we're going to cover a safer way to clear out the filament from your nozzle called cold pulling.

The idea behind a cold pull is that you set your hot end to the glass transition temperature of your filament. This is the temperature at which the filament is between both a solid and liquid. This allows you to pull out the filament and take any residue along with it. This works best with Nylon, ABS or PLA 3D printing filament.
Before you start: Cold pulls with a bowden tube can be tricky so if you're using a bowden extruder, remove the tube and any material in the tube before you start. After you have finished the cold pull, put the bowden tube back in.
Step 1: Heat the nozzle to printing temperature and manually feed about 10cm of filament through the hot end (where the bowden tube was). Try to keep the filament as straight as possible. Natural or clear coloured filament works best so you can see the residue when you pull it out. If your hot end is too clogged to get anything out of the hot end, take a thin wire and a pair of pliers and stick it into the tip of the nozzle to clear the blockage.
Step 2: Once you have some filament coming out of the nozzle, bring the nozzle temperature down (120C for ABS, 90C for PLA, and 100-140 for Nylon). Try to use the lowest temperature possible for this step. It should be hot enough that the filament is malleable but not so hot that it is too soft. Be sure to cut any filament off that is dripping from the nozzle before you start the pull.
Step 3: Pull on the top of the filament until you feel it start to slowly give out. If it comes out too easily and there is no residue on the end, lower the temperature. If you have trouble pulling it out, raise the temperature until it does.

You'll know you've done it right when there is a small sharp tip on the end and possibly some residue on the filament (this is most obvious when doing your cold pull with white or transparent filament).
You may have to do this several times to get all the residue out. Your last cold pull should leave you with a smooth filament piece that is clean (no dark residue) and has a noticeable bead that is the size of your nozzle orifice (like the second strand of filament shown above). Once you're convinced all the blockage has been removed, put the bowden tube back and try printing.
By following these tips, you should be able to remove your nozzle jam and hopefully prevent it from happening again. Happy printing!
Looking for new 3D Printing Designs? Check out 3D Files on Pinshape!
Source: https://blog.pinshape.com/5-causes-of-a-nozzle-jam-and-how-to-fix-it/
0 Response to "Pla Broke Inside Feed Delta Mini"
Post a Comment